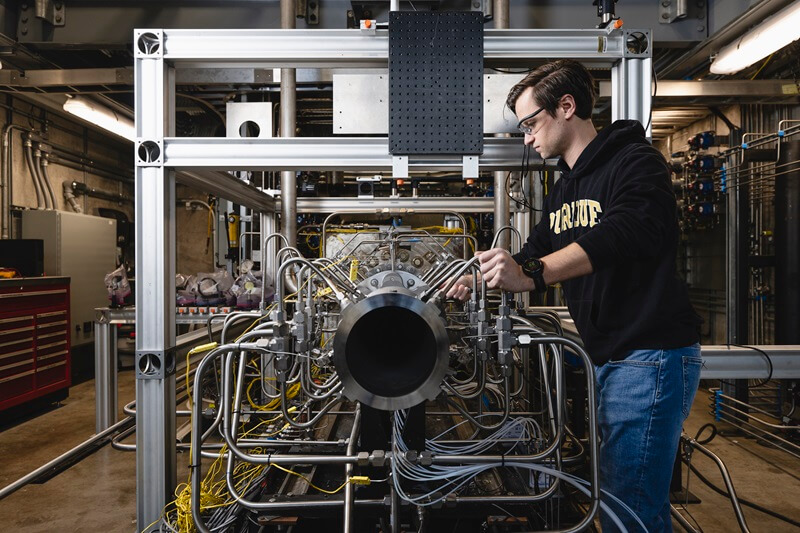
WEST LAFAYETTE, Ind. — A team of graduate students at the Purdue Applied Research Institute (PARI) successfully tested a full-scale, 3D printed scramjet, an engine that allows aircraft to travel at speeds of Mach 5 and beyond. The test, which took place at the Maurice J. Zucrow Laboratories, will provide insights that help increase the engine’s efficiency and reduce hypersonic manufacturing costs.
Greg Scofield, director of the PARI Hypersonics Lab, said the Hypersonics Advanced Manufacturing Technology Center, where the scramjet was designed and made, is one of the few university-affiliated facilities with a student-led effort to build a full-scale scramjet for testing at hypersonic-relevant conditions.
“This test demonstrates not only the level of quality of students and staff that are participating in work at PARI, but also the ability to do this work at scales that are of interest to the hypersonics community,” Scofield said. “We can design, build and test things at scales that are pertinent to commercial and defense applications.”
This student team, led by graduate research assistant Will DeVerter, produced a prototype similar in scale to the X-51A Waverider, an unmanned scramjet that completed a hypersonic flight above Mach 5 in 2010. This is significant, DeVerter said, because it is much larger than most university scramjet test articles and is comparable to systems produced by large industry players.
“It’s really difficult to simulate the conditions at that speed,” DeVerter said. “Zucrow is one of only several labs in the world with the capability to supply air and fuel at conditions requisite for full-scale scramjet propulsion.”
DeVerter and his team ignited the scramjet combustor and simulated engine operating conditions corresponding to vehicle flight exceeding Mach 5, or five times the speed of sound. This required using a combustion air heater to generate immense pressure and air temperatures above 2,000 degrees Fahrenheit. The supersonic exhaust from the heater then passed through the scramjet engine, where additional fuel was injected and ignited.
“We were very happy with the test results,” DeVerter said. “Ignition was achieved on the first attempt, and our hardware remained unscathed even after firing the engine several times. Results like that prove the efficacy of the manufacturing process.”
The scramjet was built using additive manufacturing — 3D printing — a technique that helps to reduce production costs due to less hands-on labor and faster prototyping. According to Mark Lewis, president and CEO of PARI, the high costs associated with manufacturing a scramjet stem from the combustion process and the complex cooling channels required to keep the components from melting midflight.
“Prior to additive manufacturing, those cooling channels were essentially handmade. They had to be drilled into the metal,” Lewis said. “Now you can embed those complicated geometries using computer modeling. It’s much less expensive because there’s less touch labor.”
Additionally, Lewis said that while the design of the scramjet engine is simple in concept, it’s extremely difficult to get the combustor — the part that’s responsible for generating the thrust that propels the engine forward — to properly mix the fuel and burn at high speeds. Thus, designing this component often requires significant trial and error. The additive manufacturing process reduces the amount of time it takes to go from a digital design to a physical prototype, so revamping a component can be done more quickly and efficiently.
DeVerter and his team developed the models for the entire scramjet engine, including the cooling channels and combustor. Their design then went through a series of reviews before the parts were manufactured.
“We did everything from beginning to end,” DeVerter said. “We had full control over the entire process, from designing the prototype, choosing the test objectives, running the tubes that connect the scramjet to the test stand and then, ultimately, running the test.”
A behind-the-scenes look demonstrates how much preparation goes into a successful test. First, the researchers must ensure all hardware is configured correctly, verify all the valves are in the correct position and confirm they have the necessary fuel to run the test. They also check that all the sensors are properly connected to collect data during the test. Then, prior to igniting the scramjet, they validate that the components, pressure, fuel systems and airflow are functioning as intended by running a series of “cold flow tests” that move air and gases through the components without the use of heat.
“We’re always looking at all the pressures and temperatures, making sure nothing anomalous is happening,” DeVerter said. “There’s a lot that goes into a test. Everyone sees the final product, which is some nice pictures and plots and graphs, but it’s several weeks’ worth of effort.”
And it’s an effort with a huge payoff. The results of this test enable PARI researchers to increase the efficiency of the scramjet design, such as reconfiguring the fuel injector or combustor to get the fuel to mix and burn more effectively at high speeds and improve additive manufacturing processes.
“Moving forward, we want to rapidly iterate on the design and transition this technology to industry partners,” Scofield said. “The ultimate goal is to move past the lab and into the real world.”
This effort is one of five projects funded by the Office of the Secretary of Defense’s Manufacturing Science and Technology Program, partnering with the Naval Surface Warfare Center, Crane Division, and the National Security Technology Accelerator’s Strategic and Spectrum Missions Advanced Resilient Trusted Systems.
About Purdue University
Purdue University is a public research institution demonstrating excellence at scale. Ranked among top 10 public universities and with two colleges in the top four in the United States, Purdue discovers and disseminates knowledge with a quality and at a scale second to none. More than 105,000 students study at Purdue across modalities and locations, including nearly 50,000 in person on the West Lafayette campus. Committed to affordability and accessibility, Purdue’s main campus has frozen tuition 13 years in a row. See how Purdue never stops in the persistent pursuit of the next giant leap — including its first comprehensive urban campus in Indianapolis, the Mitch Daniels School of Business, Purdue Computes and the One Health initiative — at https://www.purdue.edu/president/strategic-initiatives.
Media contact: Lindsey Macdonald, macdonl@purdue.edu